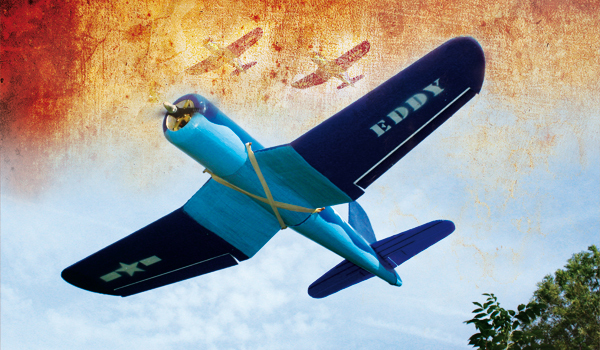
Corsair F4U Aircombat-Fighter
Zwei Eigenschaften, die ein Aircombat-Modell braucht, lauten: schnell gebaut und wendig im Flug. Irgendwann fiel mir bei den Wettbewerben auf, dass ein Modell trotz seiner hohen Bekanntheit wenig geflogen wurde, die Vought Corsair F4U. Und als Fan der TV-Serie „Pazifik Geschwader“ blieb mir gar nichts anderes übrig, als so ein Teil in Angriff zu nehmen.
Dreiseiten-Ansichten gibt es in den virtuellen Weiten des Webs ja genug, allerdings oft mit leichten Abweichungen und Verzerrungen der Maße. Mittels Vergleich der technischen Daten und der Skizzen findet man aber schnell eine passende Zeichnung. Bei Aircombat ist der Maßstab auf 1:12 festgelegt; ± Regelwerk-Toleranzen. So errechnete ich für meinen Piraten anhand der Ansichten die entsprechenden Maße. Jetzt folgt der meiner Meinung nach wichtigste Schritt: Das gedankliche Zerlegen des Modells in möglichst wenige, einfach reproduzierbare Einzelteile, ohne sich dabei zu weit vom Original zu entfernen. Ich bin nämlich anerkanntermaßen faul und aus wenigen Teilen baut man einfach schneller.
Da ich sowohl eine Fräsmöglichkeit auf einem umgebauten Flachbettplotter habe als auch glücklicher Besitzer einer HSSS (HansSeyboldtStyroSchneide) bin, wurde der gesamte Bausatz auf diese Möglichkeiten hin ausgelegt. Natürlich kann man die wenigen Holzteile auch von Hand aussägen und die Styroteile mittels Schablonen ausschneiden. Hinweise und Vorlagen dazu finden sich im Download-Plan, der kostenlos für private Zwecke von der Internetseite www.modell-aviator.de heruntergeladen werden kann.
Formgebend
„Entwickeln Sie um das stärkste Triebwerk die kleinste Flugzeugzelle“, hieß damals der Entwicklungsauftrag für die Vought Corsair F4U. So entstand das „fliegende Teerfass“, wie dieser Zweite-Weltkriegs-Jäger auch scherzhaft aufgrund seiner Rumpfform genannt wurde.
Das Hauptbrett im vorderen Rumpfteil nimmt Motor, Akku, Empfänger und Höhenruder-Servo auf. Es wird aus zwei Teilen auf 6 Millimeter (mm) gedoppelt. Das obere, breite Teil fasst in die im Rumpf eingeschnittene Nut, durch die gleichzeitig der Motorsturz vorgegeben ist. Im Hauptbrett ist zugleich der Seitenzug des Motors eingebaut. Daher muss hier folgendes beachtet werden: schmales Brett unten, Seitenzug nach rechts. Das mit den Dübeln verschraubte GFK-Motor-Kreuz erleichtert auch eine passgenaue, spannungsfreie Verklebung des Motorhalters. Alle Teile werden mit PU-Leim in einem Zug mit dem Hauptbrett verklebt. Bei Bedarf kann man anschließend für besonders lange Motoren den Ausschnitt anpassen und die Einbauten am Hauptbrett vorbereiten.
Zur Verklebung im Rumpf schiebt man das Hauptbrett von hinten nach vorne bündig ein. Gleichzeitig schließt man den Rumpf oben. Im Heckteil schaffen zwei kleine Kerben Platz für das hineinragende Hauptbrett. Indem man über die Nähte peilt, kann man beim Ankleben des Heckteils den geraden und winkligen Sitz sicherstellen. Der vordere Holzring schafft etwas Stabilität für rauere Landungen. Für alle Klebungen wird PU-Leim verwendet.
Tapezierer
Mittels Schleifpapier in 80er- und 180er-Körnung bringt man den Rumpf schnell in Form. Das gilt besonders
für das Abrunden der Rumpffront. Die durch das Hitzeschneiden glasige Oberfläche des Styros sollte auf jeden Fall überall durch Glattschleifen aufgebrochen werden. Dann hält die Bespannung mit dem Lack-Leim-Wasser-Gemisch später besser.
Bevor der Rumpf mit dem Packpapier tapeziert wird, muss noch rechts und links Gitterband als Verstärkung aufgebracht werden – ebenso direkt vor und hinter der Flächenauflage. Hier sogar doppeltes Gitterband, damit die Holzdübel für die Flächengummis genug Halt haben. Das oftmals recht widerspenstige Gitterband kann man mit Hilfe von Sprühkontaktkleber an Ort und Stelle fixieren. Es ist darauf zu achten, dass sich die Gitterbänder ausreichend gegenseitig überlappen. Jetzt wird aus Packpapier je ein rechtes und linkes Heckteil sowie rechtes und linkes Vorderteil mit reichlich Zugabe zum Überlappen ausgeschnitten.
Die benötigte Lack-Leim-Wasser-Mischung mixt man aus ungefähr 30 Prozent wasserlöslichem Parkettlack, zum Beispiel Swing Color Holz- und Korksiegel, 30 Prozent Ponal Classic und 40 Prozent Wasser. Damit geht man ähnlich wie beim Tapezieren vor. Die Papierteile werden zuerst auf einer wasserfesten Unterlage eingestrichen und können dort einweichen, während man die Styroteile einpinselt. Wenn beim Bespannen der Styroteile Falten im Papier, beispielsweise durch Rundungen entstehen, sollte man an diesen Stellen mit einer Schere einschneiden und das Papier übereinanderlegen. Im Gegensatz zu Falten sieht man das hinterher kaum. Vorne an der Motorhauben-Rundung ist das ganz wichtig. Hier sind sie kammartig in kleinen Abständen von etwa 8 bis 10 mm ringsherum einzuschneiden – beim Kleberaufpinseln nicht kleinlich sein.
Erhaben
Ganz geknickt kommen die Tragflächen der Corsair daher. Wegen des starken Antriebs kam beim Original ein mächtiger Propeller zum Einsatz, der den Boden umgepflügt hätte. Um die nötige Bodenfreiheit zu schaffen, wurde der Rumpf mittels des Knickflügels einfach angehoben.
Im Modell ergeben sich daraus fünf Flächenteile, die, um deckungsgleiche Übergänge zu gewährleisten, jeweils mit gegengleichen Winkeln geschnitten sind. Am inneren Rumpfflügel zum Mittelflügel jeweils 11 Grad beziehungsweise 101 Grad absolut. Vom Mittel- zum Außenflügel jeweils 14 beziehungsweise 76 Grad absolut. Daraus ergibt sich eine V-Form von 6 Grad pro Seite. Dieser Winkel entspricht dem Original.
Beim Verkleben der Flächenteile mit PU-Leim ist auf einen korrekten Profilverlauf zu achten, um hier Verzüge und in sich verwundene Flächen zu vermeiden. Der Holm besteht aus vier Teilen, wobei die Schäftungen in der Mitte überkreuz geklebt werden. Weißleim ist hier die sicherste Klebeverbindung, man sollte allerdings auf ausreichend Pressdruck achten. Diese Holme haben bei mir bisher auch die zackigste Wende und jeden Vollgas-Looping ausgehalten. Wer der Sache nicht traut, kann hier aber gerne noch 0,8-mm-Flugzeugsperrholz im Mittelbereich des Holms anbringen. Da ich mir denke, dass etwas, was wenig Ecken und Kanten hat auch nicht so schnell bricht, verschleife ich auch den Holm. Vor allem die unteren Knicke, auf denen man auch landet, werden jetzt schon dem Original ähnlich verrundet. Das bauchige Rumpf-Unterteil wird erst nach dem Bespannen der Fläche auf diese aufgeklebt und papierbespannt.
Ausschachten
Um Holmausschnitte, Servo- oder Kabelschächte in Styroteile einzubringen, verwende ich immer gerne eine Lötpistole, in die ich statt der Lötspitze Kupferformdrähte einspanne. Solche Kupferformdrähte fertige ich aus normalem 1,5er-Verlegekabel. Dazu werden zirka ein Meter abisoliert und die Enden etwa 5 mm abgewinkelt. Das eine Kabelende wird in einen Schraubstock und das andere in einen Akkuschrauber gespannt. Leicht stramm ziehen und dann rechtsrum drehen, dabei bis fünf zählen – nicht Umdrehungen, einfach willkürlich zählen. Linksrum bis zehn und wieder rechtsrum bis fünf zählen. So erhält man einen härteren, absolut geraden Kupferdraht, aus dem man im Maß passende und haltbare Formen biegen kann. Mit Hilfe des selbst hergestellten Schneiddrahts lässt sich ein passgenauer Ausschnitt in die Fläche einbringen, in der der Holm auch mit wenig Kleber sehr gut hält. Aber Achtung: Die Servoschächte werden erst nach dem Lackieren ausgeschnitten. Die Kabeldurchführungen steche ich mit einem erhitzten 3-mm-Stahldraht unter der Papierbespannung durch, was wegen der Knickflächen ganz gut geht.
Nachdem die Randbögen und die gesamte Fläche geschliffen wurden, wird diese an neuralgischen Punkten mit Gitterband verstärkt. Dazu den Holm unten über die ganze Spannweite mit Gitterband abdecken und auch Gitterband um die Nasenleiste legen. Hier helfen ebenfalls einige Sprühkleberflecken, um dieses widerspenstige Zeug zu bändigen. Damit ist die Fläche zum Papierbespannen vorbereitet.
Verpackungskunst
Wegen des Knickflügels benötigt man aus dem Packpapier fünf Ober- und fünf Unterteile, je drei kleine für die Mittelflügel und zwei für die Außenflügel. Auf die Außenflügel legt man bündig mit den Endleisten die Glasfaserbänder auf, die als Querruder-Scharnier dienen. Das Papier hier, wie beim Rumpf auch, gut überlappen lassen und bei den Profil- und den Randbogenrundungen einschneiden.
Die Fläche unbedingt in einem Arbeitsgang komplett bespannen. Ich bespanne immer zuerst die Oberseite und lege das Papier auf die Unterseite um. Das Papier der Unterseite lege ich mit Abstand zur Endleiste und zum Randbogen auf, hier schlage ich nur an der Nasenleiste nach oben um.
Die Querruder werden nach dem Lackieren 310 mm breit – bis knapp in den Randbogen – und innen 40 sowie außen 35 mm tief von unten keilförmig eingeschnitten. Dabei so vorsichtig vorgehen, dass der Glasfaserstreifen nicht beschädigt wird. Rechts und links schneidet man zirka ein Millimeter frei.
Plastik statt Jute
Die Flugrichtung wird maßgeblich von den Leitwerken bestimmt. Bei meiner Aircombat-Corsair bestehen diese aus Coroplast-Doppelstegplatten und entstanden nach den Schablonen aus dem Downloadplan. Dieses Material ist leicht, sehr stabil und einfach zu verarbeiten. Die Scharniere stellt man her, indem man aus der Unterseite zwischen zwei Stegen das Material herausschneidet. Hier kann dann auch der U-förmige Drahtverbinder eingelegt werden, dessen Spitzen in die Ruderhälften gesteckt werden.
Rein äußerlich macht natürlich die richtige Farbgebung schon was her. Da die Corsair von den unterschiedlichsten Geschwadern in vielen Teilen der Welt geflogen wurde, bietet eine Internetsuche bestimmt jedem das Farbschema seines Geschmacks. Für den Combateinsatz wählt man eine Lackierung bis 1945 in Verbindung mit den entsprechenden Hoheitszeichen und eventuell einer hübschen Nose-Art-Lady.
Powerfrage
Die inneren Werte sind durch den Einsatzzweck bestimmt. Zum Funfliegen reicht ein 3s-LiPo-Antriebsstrang mit einem 110-g-Brushlessmotor mit etwa 1.200 Umdrehungen in der Minute pro Volt (U/min/V) an einem 9 × 5-Zoll-Propeller aus. Aircombat-mäßig kann man Motoren bis 160 g und 1.000 U/min/V an 4s-LiPos mit 4.400 Milliamperestunden Kapazität und einem 10 × 6-Zoll-Propeller austesten. Diese Combo erlaubt Fight-Geschwindigkeiten bis 110 Stundenkilometer. In dem Fall ist die Propzahl, die Einsatzzeit von mindestens sieben Minuten und das Mindestgewicht zu beachten.
Der Schwerpunkt liegt bei 70 mm. Die Ausschläge betragen beim Höhenruder ± 20 mm und beim Querruder differenziert +16/-8 mm bei 30 Prozent Expo. Gerade in die Luft geschoben, geht der Pirat wie auf Schienen. Mehrere Piloten haben bisher bestätigt, dass die Corsair keinerlei Zickigkeiten besitzt, immer folgsam am Ruder liegt, schnell und wendig geflogen und sehr langsam und überschaubar zur Landung reingeholt werden kann. „Zu langsam“ wird mit Nase runter und Fahrt aufnehmen quittiert, ohne Abriss- oder Trudelneigung.
Belohnung
Lohnenswert war die aufwändige Denksportaufgabe der Entwicklung für mich ganz bestimmt. Das markante Flugbild, die guten Flugeigenschaften und die sehr gute Combat-Tauglichkeit lassen immer wieder Spaß an der Corsair aufkommen. Das hat dann auch dazu geführt, dass ich auf dieser Grundlage einen recht konkurrenzfähigen Reno-Racer „Red Corsair“ F2G für das Combat-Racing daraus entwickelt habe. Man sieht, mit ein bisschen Hirnschmalz und Fantasie lässt sich bestens der eigene Horizont erweitern.